在供应链的战场上,信息断层就像隐形的绊马索,随时可能让整个体系陷入混乱。企业微信的定制开发如同一把精准的手术刀,正在切开传统供应链的“信息肿瘤”,让生产、物流、供应商三大核心环节实现真正的血脉相通。从车间工单的实时穿透到物流车辆的全程追踪,一场静默的协同革命正在重构商业世界的连接逻辑。
生产工单的透明革命
传统生产工单一旦离开办公室,就仿佛掉进了信息黑洞。定制化的解决方案将纸质工单转化成流动的数据链,车间主任的手机屏幕成了指挥中心——设备状态、物料消耗、工序进度这些原本分散在十几个系统的数据,现在像拼图一样实时拼接完整。当某条生产线突然卡壳,预警信息会同时弹到维修组长和采购负责人的聊天窗口,连带推送备用设备的位置图和供应商的应急联系方式。
这种透明化不止于工厂围墙之内。通过打通供应商的生产系统,原料库存数据每半小时自动刷新一次。当系统预判到关键物料只能支撑未来五小时的生产时,会绕过人工审批直接触发补货指令,甚至根据历史数据智能分配订单比例——既能避免独家供货的风险,又能用竞争机制压低采购成本。工单状态的每一次变化,都像投入水面的石子,在整个供应链网络激起智能反应的涟漪。
物流网络的数字镜像
过去追踪一批货的位置,就像在迷宫里找出口——电话、邮件、系统来回切换,拿到手的还是过时信息。现在每辆货车都成了移动的数据发射塔,GPS定位、车厢温湿度、货物倾斜角度这些数据,通过物联网模块实时回传到企业微信。仓库主管喝着咖啡刷手机,就能看到全国运输网络的“心电图”:哪些路段正在堵车、哪些冷链车温度异常、哪些中转仓即将爆仓,所有关键节点一目了然。
退货流程的改造更显功力。客户在企业微信提交退货申请的瞬间,系统已经生成带区块链溯源码的电子面单。包裹还没到仓库,质检标准、退款规则、供应商责任判定方案都已经准备就绪。当扫码枪“滴”的一声响过,后续的财务流程、供应商考核、质量改进建议会自动串联启动。这种闭环管理,把原本需要三天扯皮的退货流程,压缩成两小时就能走完的流水线。
供应商协同的破冰行动
和供应商打交道最怕什么?不是讨价还价,而是信息不对等的猜疑游戏。定制开发的供应商门户打破了这道冰墙,登录后看到的不是冷冰冰的采购订单,而是动态的需求全景图——未来三个月的预测需求、产线改造计划、质量投诉趋势,这些原本藏着掖着的数据现在成了共同决策的筹码。有家配件厂老板说,现在看企业微信就像看自家工厂的监控大屏,连客户的新品设计动向都能提前嗅到味道。
质量问题处理更是颠覆传统。生产线上刚检出批次不良,带视频分析的质检报告已经同步推送到供应商技术群的@所有人消息里。双方工程师不需要约会议室,直接在文档协作区写问题分析、传改进方案、批注工艺参数,解决问题的速度比过去打电话发邮件快了不止三倍。这种透明到毛孔的协作,让供应商从被动的订单执行者,变成了能主动提出工艺优化的合作伙伴。
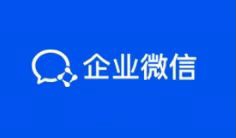
数据中枢的智能调度
真正的高手玩供应链,玩的是数据预判。通过清洗ERP、MES、WMS等系统的历史数据,定制开发的智能中枢能捕捉到人眼看不见的规律。比如每周三下午的包装线效率会下降5%,不是因为工人偷懒,而是物料配送车的路线和电梯使用高峰撞了车。系统自动生成的优化方案里,连包装箱的摆放顺序都给出了可视化指导图。
风险预警系统更像是未卜先知的预言家。当系统监测到东南亚某港口的吞吐量连续三天低于平均水平,会立即启动应急预案推演——比较空运转陆运、切换港口、启用应急库存等不同方案的成本时效比。管理层收到的不是干巴巴的预警通知,而是带着模拟数据的决策选项包,每个选择后面都跟着具体的执行步骤和预期结果。
协同网络的自我进化
好的供应链系统不应该只是工具,而应该具备学习能力。每次异常事件的处理过程都会被系统拆解成案例库,下次遇到类似情况时,操作界面会自动弹出历史解决方案的要点提示。有家制造企业的物流经理发现,系统最近开始提醒他特定季节的货车保养周期需要提前——这是算法从过去三年的抛锚记录里挖出的隐藏规律。
权限管理也玩出了新花样。遇到临时项目需要外部专家支持时,不用再折腾复杂的账号申请流程。通过“权限乐高”模块,五分钟就能拼出个临时协作空间——研发图纸可以看不能下,质量数据能读不能改,项目结束权限自动回收。这种收放自如的灵活性,让跨企业协作不再需要“用人不疑”的豪赌。
当生产线的设备振动数据开始影响物流车的发车时刻表,当供应商的质量改进建议能直接触发工艺参数调整,这样的供应链已经不再是简单的链条,而是进化成了有生命的协同网络。企业微信的定制开发就像给这个网络装上了神经系统,让每个环节的波动都能转化为整体的优化动力。信息孤岛的打破只是表象,更深层的变革在于组织协作基因的重构——在这里,数据代替了扯皮,透明消解了猜忌,而效率提升成了水到渠成的自然结果。